Premium 3-ply double vulcanized nitrile rubber attack hose
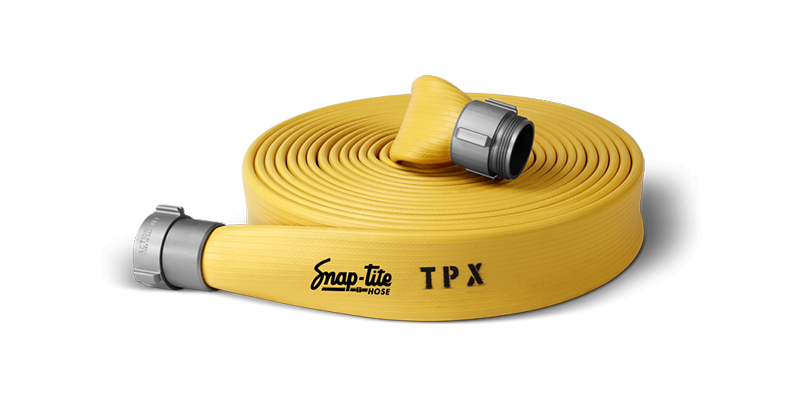
SUMMARY:
Hose shall be manufactured in the United States to NFPA 1960 and ISO 9001:2015 quality management system standards and craftsmanship. Hose must meet or exceed NFPA testing requirements. The hose shall be free from defects in materials and workmanship.
MANUFACTURER:
The hose must be domestically sourced, woven, extruded, assembled, coupled, and tested in an ISO 9001:2015 certified facility in the United States, which shall constitute the product’s country of origin.
JACKET:
The hose must be woven with 100% synthetic yarns with the reinforcement jacket woven in a circular twill weave configuration. The nitrile rubber cover should be extruded independently, inserted inside the tight weave reinforcement, vulcanized, then turned inside out.
LINING:
The liner (waterway) must be a nitrile rubber. No rubber applied by a hot melt process into or onto the inner liner surface of the reinforcement fabric will be permitted, nor will the use of an adhesive or backing to secure a tube lining.The liner must be inserted into the jacket and vulcanized to bond all three plies. The liner must be guaranteed not to delaminate for the life of the hose and manufactured in the United States.
TEMPERATURE FLEXIBILITY:
The hose must remain flexible at temperatures -40° F to 200° F (-40°C to 93°C).
WEIGHT:
Hose must be measured dry coupled 50’ lengths. Weight must not exceed:
1-3/4” - 19 LBS
2” - 24 LBS
2-½" - 33 LBS
3” - 37 LBS
SERVICE, PROOF, BURST PRESSURES:
1-¾" and 2” hose must meet the following pressures; service (400 psi), proof (800 psi), and burst (1200 psi). 2-½" hose must meet the following pressures; service (330 psi), proof (660 psi), and burst (1000 psi). 3" hose must meet the following pressures; service (300 psi), proof (600 psi), and burst (900 psi).
FLOW & FRICTION LOSS:
When requested, friction loss test results shall be provided to the customer.
KINK RESISTANCE:
Hose must meet doorway kink resistance test at 50 psi, with the following specifications based on size:
1-3/4” - 24” bend radius.
2-½" - 30” bend radius.
ABRASION RESISTANCE:
The hose must withstand a minimum of 8,500+ abrasion cycles (Taber H-22 wheel) without jacket damage.
STANDARDS:
The hose must meet or exceed all performance requirements of NFPA 1960 (1961).
QUALITY ASSURANCE PROVISIONS:
Hose manufacturer must maintain a current ISO 9001:2015 certified Quality Management System, covering the entire manufacturing process—from design and raw material procurement to weaving, extrusion, assembly, testing, and delivery.
HYDROSTATIC TESTING:
Each coupled hose must undergo hydrostatic proof testing by the manufacturer and meet NFPA 1961 (latest edition) standards. Test certification must be provided with each length.
IDENTIFICATION AND MARKING:
Each hose must have a unique barcode on the coupling per NFPA 1962, linking to manufacturing and test records. The manufacturer must maintain a customer-accessible electronic database for the hose’s service life. Hoses must also be marked with the manufacturer’s name, date, origin, and “Service Test to ___ PSI per NFPA requirements.”
COUPLINGS:
All coupled hose must be assembled with couplings sourced in the United States and must meet or exceed NFPA 1963 - latest edition.
WARRANTY:
The fire hose must have a two-year “all hazard” warranty against any damage incurred during firefighting operations, a ten-year warranty against manufacturing defects, and a lifetime warranty against liner delamination.