Premium extruded thru-the-weave thermoplastic polyurethane supply hose
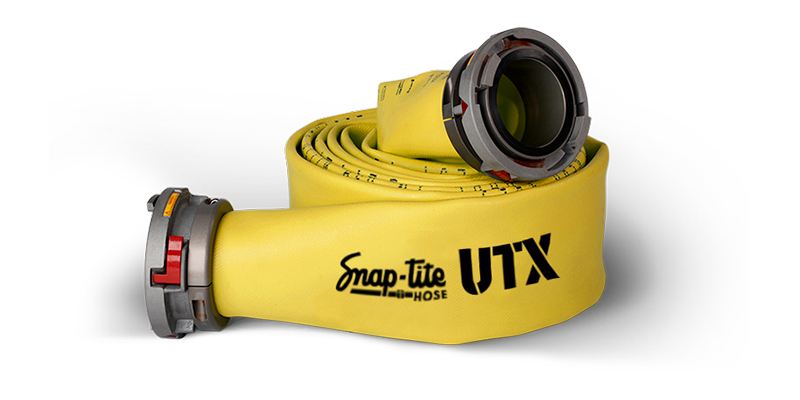
SUMMARY:
Hose shall be manufactured in the United States to NFPA 1960 and ISO 9001:2015 quality management system standards and craftsmanship. Hose must meet or exceed NFPA testing requirements and be free from defects in materials and workmanship.
MANUFACTURER:
The hose must be domestically sourced, woven, extruded, assembled, coupled, and tested in an ISO 9001:2015 certified facility in the United States, which shall constitute the product’s country of origin.
JACKET:
The hose must be woven with 100% synthetic yarns with the reinforcement jacket woven in a circular twill weave configuration.
LINING:
The lining material shall be thermoplastic polyurethane extruded thru-the-weave. The thermoplastic polyurethane must completely encapsulate all the yarns and fibers on both sides of the reinforcement jacket and penetrate through the jacket. No thermoplastic polyurethane applied by a hot melt process into or onto the inner liner surface of the reinforcement fabric will be permitted, nor will the use of an adhesive to secure a tube lining. The liner must be guaranteed not to delaminate for the life of the hose and manufactured in the United States.
TEMPERATURE FLEXIBILITY:
The hose must remain flexible at temperatures -50° F to 160° F (-45°C to 71°C).
POTABLE WATER:
The hose shall be approved for use with potable water.
WEIGHT:
Hose must be measured dry coupled 50’ lengths. Weight must not exceed:
4” - 70 LBS
5” - 93 LBS
SERVICE, PROOF, BURST PRESSURES:
Hose must meet the following pressures; service (200 psi), proof (400 psi), and burst (600 psi).
FLOW & FRICTION LOSS:
When requested, friction loss test results shall be provided to the customer.
ABRASION RESISTANCE:
The hose must withstand 100,000 abrasion cycles (Taber H-22 wheel) without jacket damage.
STANDARDS:
The hose must meet or exceed all performance requirements of NFPA 1960 (1961).
QUALITY ASSURANCE PROVISIONS:
Hose manufacturer must maintain a current ISO 9001:2015 certified Quality Management System, covering the entire manufacturing process—from design and raw material procurement to weaving, extrusion, assembly, testing, and delivery.
HYDROSTATIC TESTING:
Each coupled hose must undergo hydrostatic proof testing by the manufacturer and meet NFPA 1961 (latest edition) standards. Test certification must be provided with each length.
IDENTIFICATION AND MARKING:
Each hose must have a unique barcode on the coupling per NFPA 1962, linking to manufacturing and test records. The manufacturer must maintain a customer-accessible electronic database for the hose’s service life. Hoses must also be marked with the manufacturer’s name, date, origin, and “Service Test to ___ PSI per NFPA requirements.”
COUPLINGS:
All coupled hose must be assembled with couplings sourced in the United States and must meet or exceed NFPA 1963 - latest edition.
WARRANTY:
The fire hose must have a two-year “all hazard” warranty against any damage incurred during firefighting operations, a ten-year warranty against manufacturing defects, and a lifetime warranty against liner delamination.